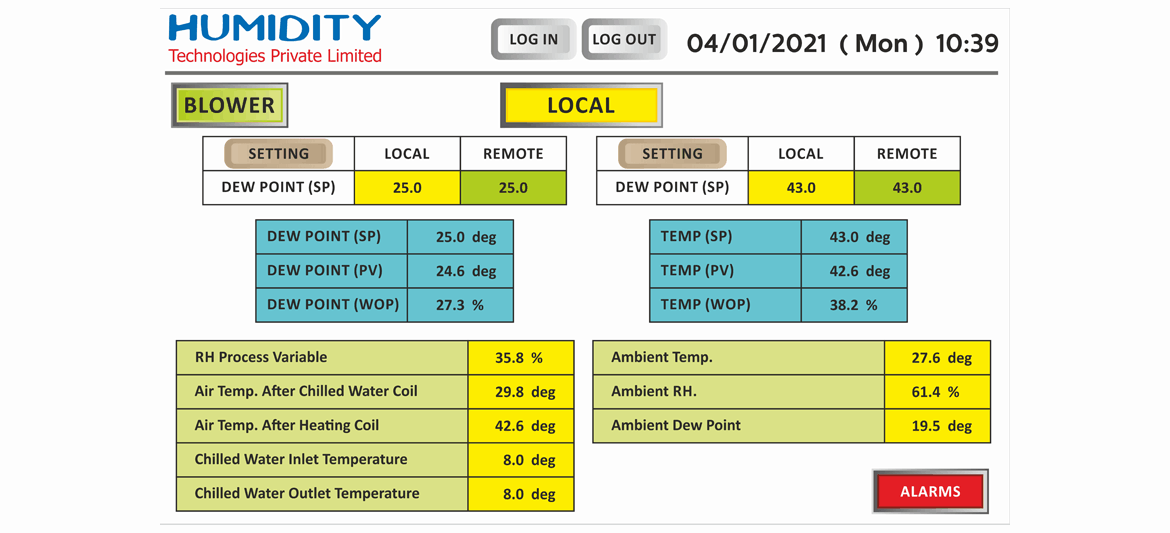
A poorly understood area in humidity control is process equipment such as Coaters, Fluidized Bed Equipment etc.
Moisture Control of the FBE is fundamental to their operation, however there is the variable input effect of ambient relative humidity that can greatly affect the process on a day-to-day basis UNLESS steps are taken to provide stable temperature and relative humidity irrespective of incoming air parameters.
A clear understanding of the ambient Temperature and humidity vis-a-vis the RH and temperature required for the process helps obtain consistent results. This relationship is often not clearly or completely understood by many equipment designers and manufacturers – let alone the users.
Usually the FBE equipment supplier is entrusted with the responsibility to supply the equipment as a complete package including the air handling unit. However, considering the criticality of the process, it is advisable that a company specialized in the process air treatment be employed to ensure that the air treatment system developed is not only able to maintain constant supply air temperature and humidity irrespective of outside air condition but is also energy efficient and meets the regulatory requirements of cGMP.
As the process air is not recirculated, energy costs for the air handling system are very high. To achieve process efficiency and product consistency, the equipment as well as the control systems need to be matched correctly to ensure air is supplied at or near the required conditions. A well-designed system with integrated control ensures better yield and lower rejections as well as quicker processing times thus saving energy. The payback period is extremely short – with investment often recovered in the first batch itself.
Our capabilities are demonstrated in the following case study:
Case Study
The Problem
A leading pharmaceutical company had issues in tablet coating performance as their existing Air Handling System supplied by an OEM was unable to provide consistent humidity control – at low as well as high dew point. Having successfully demonstrated our capabilities in humidification, we were asked to provide a complete solution for this particular coating machine. To achieve stable humidity, a dew point control system was planned.
The desired conditions were:
- Condition 1: 20 O C DB temperature and 16 O C Dew Point requiring cooling and dehumidification.
- Condition 2: 43 O C DB temperature and 25 O C Dew Point requiring heating and humidification.
On inspection it was observed that the cooling coil was undersized and humidification system was not provided at all.
The Solution
The existing Air Handling System was replaced with a correctly designed cooling coil as well as a humidification system to generate clean steam using boiler steam as energy source. An independent programmable controller was installed near the Air Handling System with a control logic to accurately control the temperature and humidity. The installed control system was integrated with the process PLC to enable the users to set their required parameters from the coating machine.
The control system provided also included diagnostics for quick resolution of any operational issues.
The system was able to control both – the DB temperature as well as Dew Point within 0.2O C
- A trial was taken at following different conditions:
Temperature , O C |
---|
65 |
55 |
50 |
45 |
40 |
20 |
Dew Point, O C |
---|
16 |
25 |
20 |
22 |
20 |
16 |
It was observed that the variation did not exceed + 0.3O C over the range of conditions.